Basement – Sliding Door Project
So, I’ve been doing a fair number of projects, but writing about them isn’t one of those projects. Some of it has been improving the basement a bit. Part of the slowness of the basement work is because it occasionally floods a bit. Not really “standing in water” flooding, but “there is a puddle that keeps coming” flooding.
It’s annoying, but I’ve been working to fix it. The house originally didn’t have any downspouts on the gutters, I added those. I’ve added extensions to the gutters to direct water away. I added a new downspout near the area where the water seems to come from to help direct it away more. I cut out some drywall in the underside storage area and pulled the bottom step off of the stairs to fill in some ugly crack-ish spots in the area where the water comes from. At this point, I am waiting for more heavy rain to see if some of this has made any real difference. So far the cement fill seems to have done the best. It’s tricky to describe but basically, the water still came in, but it came in waaaay less and in a slightly different place. So I’m getting there.
I’m not really here to discuss the flooding though. It has affected some decisions on how to make the basement nicer, like I am not going to add Drywall walls like I wanted to. And no carpet, though that was out anyway, because the cats are assholes (We also replaced all of the upstairs carpet with vinyl plank flooring).
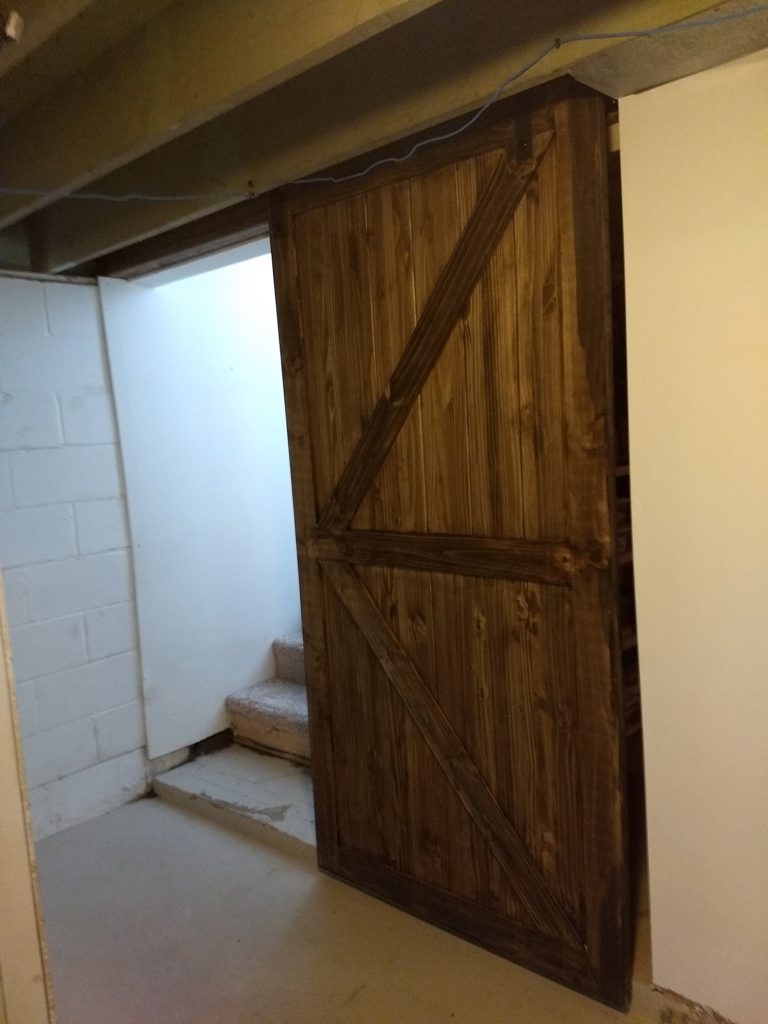
One fairly simple project was adding a door. In this case, I put in a sliding barn door style door. My wife wanted to put in a real door but I wasn’t keen on that since there isn’t really a good place for it to open to. The door itself had a couple of motivations behind it.
One, the basement is divided into two halves. One half is semi finished and “nicer” and it’s where I keep my computer and collection of stuff and there is a TV and couch with game consoles and my son has a corner that is his bedroom area when he is around. The other half is under the “original house”, it’s rough, the ceilings are a little low, and there is more duct work and such hanging from the ceiling. We use it for storing all sorts of stuff. It’s really great for that.
The “underside” half is ugly though. I wanted the door to be able to block it out, mostly for aesthetic reasons.
The other purpose of the door is to be able to lock the cats in the basement when we have guests over. My parents and my wife’s parents are all allergic to the cats. We lock some of them in bedrooms, we also lock some of them in the small sunroom/office area upstairs. Sometimes we would lock them in the basement by blocking the stairs with a giant cork board we have that doesn’t really have a home.
Now, we can use the door. It slides between the two openings, stairs and underside storage to block off either one.
One concern was air flow from the storage area, so the door can also be positioned in the middle, which is where it usually sits, so air can flow in and out both sides. It also lifts off easily if I needed to remove it.
The door itself isn’t anything complicated. I could have built a door but I opted to just buy one, though the door was pretty pricey since it needed to be extra wide. The roller kit is a low profile barn door kit, easy enough to install and it nestles up into the floor joist ceiling. The tricky part was that the floor joist didn’t reach the edge of the opening, so I had to screw a couple of 2×4 stand offs to the floor joist to get the door to sit int he proper place. This also meant adding some 2×4 lifts under the stand off to support the immense weight of the door.
I also ended up with an issue of the door rolling slightly. I am not sure if it’s the house or if the rail is a little off (probably a little of both) but the door slides towards the stairs on it’s own. Not very quickly, but it does move.
I solved this with magnets, at the suggestion of my uncle. I didn’t really want an ugly latch that would also potentially end up in the way of the door sliding or people walking. I bought some block magnets and some double sided Gorilla tape (I originally used Command Strips but they were too weak). I stuck a larger magnet to the wall, then two smaller magnets on one end and the center of the door. This allows the door to hold it’s position when blocking the stairs or when positioned halfway.

This project isn’t quite done. I may also add an L bracket of some kind in the center of the door, to hold the door from being leaned outwards, and I want to add a roller on the backside to the whole action is smoother. the way things are, if the cats get determined, they can push the door enough to get it to release from the magnet and escape from the basement.
I also need to adjust that network cable because it’s kind of just there and ugly.
Josh Miller aka “Ramen Junkie”. I write about my various hobbies here. Mostly coding, photography, and music. Sometimes I just write about life in general. I also post sometimes about toy collecting and video games at Lameazoid.com.